How Do You Calibrate a Diaphragm Pressure Gauge?
In many industrial systems, pressure measurement is vital. It helps ensure the safety and efficiency of processes. Among various types of pressure gauges, the diaphragm pressure gauge is common.
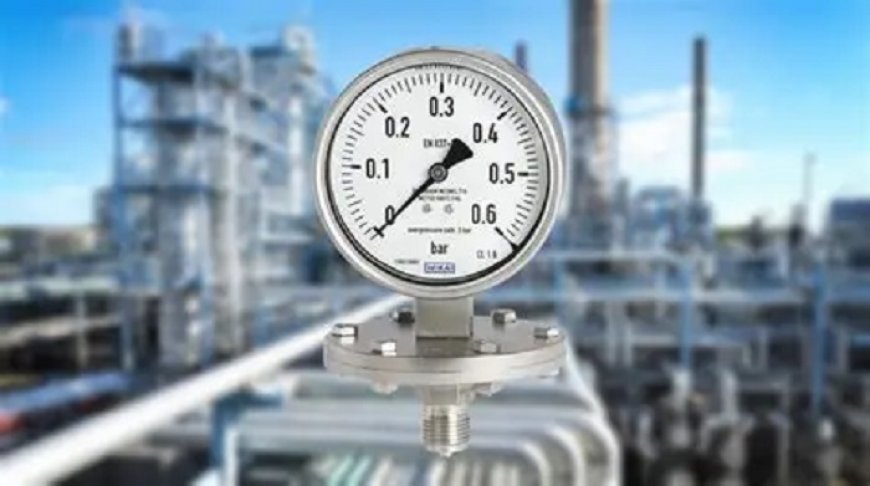
In many industrial systems, pressure measurement is vital. It helps ensure the safety and efficiency of processes. Among various types of pressure gauges, the diaphragm pressure gauge is common. It is especially useful when measuring low-pressure ranges or when the fluid is corrosive or viscous. This type of gauge uses a flexible diaphragm to detect pressure changes and transmit them to a pointer on the dial.
Over time, the accuracy of a diaphragm pressure gauge can drift. This happens due to mechanical wear, exposure to harsh chemicals, or long-term usage. Therefore, regular calibration is necessary. Calibration helps maintain precision. It ensures the gauge reflects the actual pressure values in the system.
This article will explore how to calibrate a diaphragm pressure gauge. The procedure involves a detailed understanding of the gauge's function, the calibration setup, and the proper steps. Every action must be performed with care and attention to detail. The goal is to make the diaphragm pressure gauge accurate and reliable again.
What Is a Diaphragm Pressure Gauge?
A diaphragm pressure gauge uses a thin, flexible membrane called a diaphragm. This diaphragm deflects in response to pressure applied to one side. The amount of deflection corresponds to the applied pressure. This motion is transferred through a mechanical linkage. It moves the pointer on the dial.
These gauges are ideal for low-pressure applications. They also suit processes that involve dirty, corrosive, or viscous fluids. Because the diaphragm isolates the sensing mechanism from the process fluid, it provides durability. It also allows for sanitary design in food and pharmaceutical industries.
Why Calibration Is Necessary
Every pressure gauge, including a diaphragm pressure gauge, can lose accuracy. This happens due to temperature fluctuations, vibration, pressure spikes, or aging components. If not calibrated regularly, the readings may deviate from actual values. This could lead to unsafe operating conditions, poor process control, or equipment damage.
Calibration ensures that the gauge reads correctly across its full scale. It verifies whether the pointer points to the true pressure value at known reference pressures. If the reading is off, the gauge must be adjusted or repaired.
Tools Required for Calibration
To calibrate a diaphragm pressure gauge, a few tools are necessary. The most important is a known and trusted pressure standard. This standard provides accurate pressure for comparison. It can be a digital pressure calibrator or a deadweight tester.
Also required is a pressure source. This can be a hand pump for generating pressure or vacuum. Connectors and hoses are needed to link the gauge and the standard. Finally, a stable workbench and controlled environment improve consistency during the procedure.
Preparing for Calibration
Start by inspecting the diaphragm pressure gauge. Look for any signs of damage, corrosion, or leakage. If the gauge appears faulty, it may need repair before calibration. Check that the dial and pointer are clean and free to move.
Mount the gauge vertically if possible. This is the standard position for reading. Ensure that the connections are tight. Avoid air leaks, as they can affect the readings.
Zero the gauge. Make sure the pointer is at the zero mark when there is no applied pressure. If it is off, note this error before applying any pressure. This helps you understand whether the issue is with the entire scale or just the zero setting.
Applying Pressure and Taking Readings
Now apply pressure using your pressure source. Start with the lowest test point, usually 0%. Slowly increase the pressure in steps, for example: 0%, 25%, 50%, 75%, and 100% of the full-scale value. At each point, wait for the gauge to stabilize. Record the reading on the diaphragm pressure gauge and compare it to the reference standard.
Then decrease the pressure in similar steps. This helps detect any hysteresis in the gauge. Hysteresis is the difference in reading between rising and falling pressure. It tells you if the diaphragm or mechanism lags behind when returning to a previous pressure.
Repeat this process to verify repeatability. A good diaphragm pressure gauge should provide consistent readings under the same pressure conditions.
Analyzing the Results
Compare the readings from the gauge and the reference standard. Calculate the error at each point. If the errors are within acceptable limits, the gauge passes calibration. If not, correction is needed.
There are two common types of errors. One is a linear shift, where the error is uniform across the scale. The other is non-linear error, which changes with pressure. Each type has different causes and may require different actions.
Adjusting the Gauge if Needed
If the diaphragm pressure gauge has adjustment screws, you may correct the pointer alignment. Most gauges allow for zero and span adjustments. Zero adjusts the starting point. Span adjusts the range.
To adjust the zero, remove the gauge cover and turn the zero screw. Set the pointer exactly at zero with no pressure applied. For span, apply full pressure and adjust the span screw until the pointer aligns with the correct value.
Some gauges are sealed or do not allow manual adjustment. In such cases, the gauge may need to be sent to a certified calibration lab.
Re-Testing After Adjustment
After making adjustments, repeat the calibration process. Apply pressure in steps again. Compare each new reading to the standard. Ensure that the gauge now matches the true values closely. Record the new data and confirm that the errors are within the allowed range.
If the readings are stable and consistent, the calibration is complete. Otherwise, further repair or replacement may be needed.
Documenting the Calibration Process
After calibration, complete a report. This should include the gauge model, serial number, calibration date, environmental conditions, reference standard used, and the results before and after adjustment. This record is essential for quality control and traceability.
In regulated industries, such documentation is often required. It shows that instruments are maintained correctly and are fit for service.
How Often Should You Calibrate?
The frequency of calibration depends on how often the diaphragm pressure gauge is used and under what conditions. In critical applications, calibration may be needed every three to six months. In less demanding environments, once per year may be enough.
Regular inspection can help determine the right schedule. If a gauge shows drift or erratic behavior, it should be removed from service and recalibrated immediately.
Conclusion: Precision and Safety Through Calibration
A diaphragm pressure gauge is an important tool in many industries. It provides accurate readings in low-pressure or harsh process conditions. To keep it reliable, regular calibration is essential. The process involves careful preparation, precise testing, and accurate adjustments.
By following correct steps and using proper tools, you can restore the accuracy of a diaphragm pressure gauge. This not only improves process control but also enhances safety and equipment protection. Calibration is more than a task—it is a responsibility.