Top 5 Most Commonly Used Pressure Gauges
Whether monitoring the pressure in a hydraulic system, checking tire inflation, or ensuring safety in a steam boiler, pressure gauges play a critical role in maintaining operational efficiency and safety.
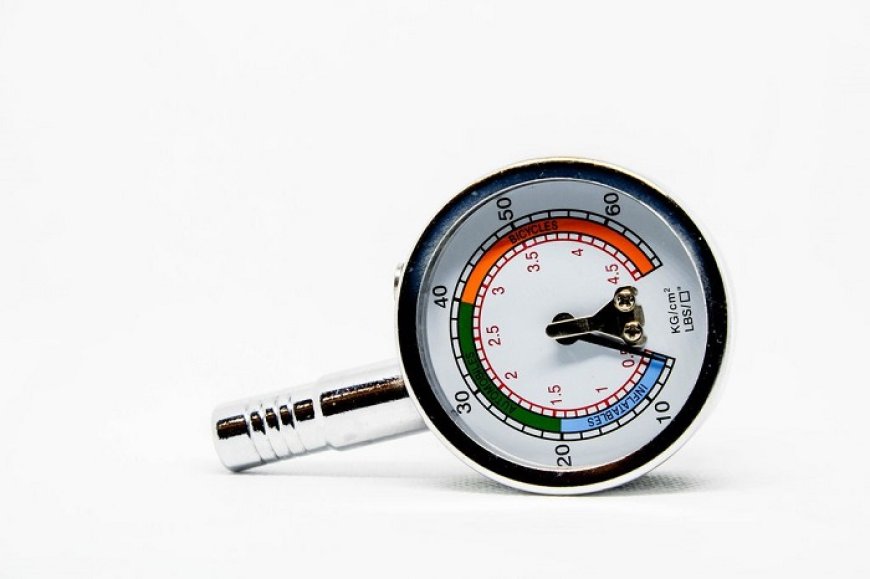
A pressure gauge is an essential device used in various industries to measure the pressure of gases and liquids. Whether monitoring the pressure in a hydraulic system, checking tire inflation, or ensuring safety in a steam boiler, pressure gauges play a critical role in maintaining operational efficiency and safety.
These devices are found across industries such as manufacturing, oil and gas, water treatment, pharmaceuticals, and HVAC systems. By converting the force exerted by fluid or gas into readable values, they allow technicians and engineers to observe conditions inside closed systems.
With technological advancements, pressure gauges have evolved in design and function. Yet, several traditional mechanical gauges still remain dominant in industrial and commercial use due to their simplicity, reliability, and cost-effectiveness. In this article, we’ll take a closer look at the top five most commonly used pressure gauges and explore what makes each type unique and indispensable.
Bourdon Tube Pressure Gauge
Most Widely Used Mechanical Pressure Gauge
The Bourdon tube pressure gauge is perhaps the most popular and recognized type of pressure gauge in the world. It operates on a straightforward mechanical principle. Inside the gauge, a curved, flexible tube (called a Bourdon tube) responds to the pressure of the fluid or gas entering it. As pressure increases, the tube straightens slightly. This movement is transferred through a linkage system to the dial needle, which indicates the pressure level.
Bourdon tube pressure gauges are used in everything from home heating systems to industrial manufacturing plants. Their popularity stems from their durability, accuracy, and wide pressure range capabilities. These gauges can measure pressures from as low as 0.6 bar to as high as 1000 bar, depending on their construction.
This type of pressure gauge is suitable for both gaseous and liquid media that are not highly viscous or crystallizing. It is also ideal for measuring pressure in high-temperature environments, thanks to its metal construction and lack of electronic components.
Diaphragm Pressure Gauge
Ideal for Low Pressure and Sensitive Media
The diaphragm pressure gauge uses a flexible membrane, or diaphragm, to sense pressure changes. When fluid or gas exerts pressure on the diaphragm, it deflects. This deflection is converted into mechanical movement, which then moves the pointer on the dial.
These gauges are perfect for applications involving corrosive, viscous, or contaminated fluids. Because the diaphragm can be made from a variety of materials such as stainless steel, Teflon, or even Hastelloy, they are often found in chemical processing plants, food manufacturing, and pharmaceutical production.
Diaphragm pressure gauges are typically used for lower pressure ranges, usually up to 40 bar. Their sealed design prevents media from contacting the mechanical parts of the gauge, reducing maintenance and increasing lifespan.
One of the significant advantages of this type of pressure gauge is its ability to measure very low pressures accurately. It is especially beneficial in situations where Bourdon tube gauges may not perform well due to sensitivity or contamination concerns.
Capsule Pressure Gauge
Designed for Measuring Very Low Pressures
The capsule pressure gauge is another highly sensitive mechanical gauge, specially designed to measure extremely low pressures of gaseous media. It works using a dual-diaphragm system, forming a capsule. When gas pressure is applied, the capsule expands or contracts, and the movement is transmitted to the dial needle.
This pressure gauge type is ideal for laboratory use, HVAC systems, or any application requiring precise low-pressure measurements. Typical pressure ranges for capsule gauges are from 0 to 600 mbar.
Capsule gauges are not suitable for liquids or high-pressure gases. However, their precision makes them invaluable for monitoring small changes in pressure where accuracy is critical. Because of their fragile nature, they are often enclosed in robust housings to prevent damage.
Differential Pressure Gauge
Monitors Pressure Differences Between Two Points
A differential pressure gauge does not measure absolute pressure like other gauges. Instead, it measures the difference in pressure between two separate points. This capability is crucial in systems such as filters, pumps, and flow monitoring where a change in pressure across components indicates performance or blockage.
This type of pressure gauge contains two pressure chambers separated by a diaphragm. The difference in pressure causes deflection in the diaphragm, which moves a pointer on a single dial. Some versions come with dual dials to display both inlet and outlet pressures.
Differential pressure gauges are commonly used in filtration systems, cleanrooms, air-handling units, and hydraulic circuits. By detecting pressure changes early, they can help operators maintain equipment efficiency and avoid system failures.
Their robust design often includes over-pressure protection and corrosion-resistant materials. They are capable of handling both liquids and gases, depending on their specific design and materials.
Bellows Pressure Gauge
Best for Precision in Narrow Pressure Ranges
The bellows pressure gauge utilizes a metal bellows element that expands or contracts in response to pressure changes. This expansion is directly linked to a pointer mechanism that indicates the pressure on a dial.
Bellows are made of thin-walled, corrugated metal tubes and offer excellent sensitivity. This type of pressure gauge is typically used for low-to-medium pressure applications, ranging from vacuum levels to about 40 bar.
Bellows pressure gauges provide high accuracy and are often used where minor variations in pressure need to be monitored carefully. Applications include gas metering, lab instrumentation, and control systems.
One unique feature of bellows gauges is their linear response to pressure changes. Unlike Bourdon tubes, which may have a non-linear response at low pressures, bellows offer consistent, accurate readings even in lower ranges. They are not as robust as Bourdon gauges but are valued for their precision.
Conclusion
Choosing the right pressure gauge for a particular application involves understanding the type of media, pressure range, environmental conditions, and required accuracy. Among the many types available, the five discussed here – Bourdon tube, diaphragm, capsule, differential, and bellows pressure gauges – are the most commonly used across industries.
Each type serves a specific purpose. The Bourdon tube remains a universal choice for general pressure measurement. Diaphragm gauges are ideal for corrosive or viscous fluids. Capsule gauges are unmatched in low-pressure gas applications. Differential gauges excel in monitoring pressure drop across filters and valves. Bellows gauges offer high precision in low-to-moderate pressure applications.
Understanding the strengths and limitations of each type ensures reliable measurement, better safety, and enhanced operational efficiency. Whether in a chemical plant, a power station, or a laboratory, the right pressure gauge is a critical component that cannot be overlooked.