Compound Gauge vs. Pressure Gauge: What Is the Difference?
Whether measuring the pressure in a steam boiler or in a refrigeration line, the right gauge must be selected. Among the many instruments available, two commonly used ones are the compound gauge and the pressure gauge.
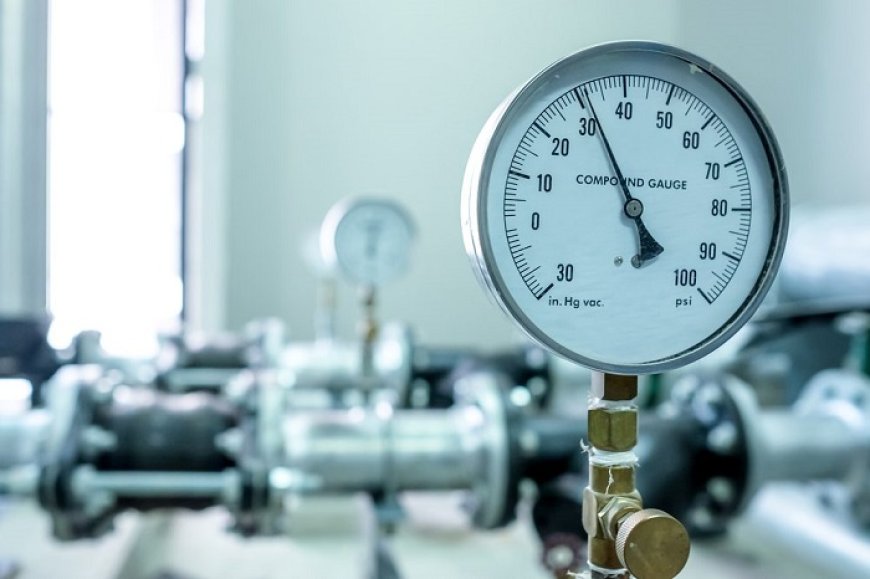
In mechanical and industrial systems, accurate pressure measurement is essential. Engineers rely on gauges to monitor the performance and safety of equipment. Whether measuring the pressure in a steam boiler or in a refrigeration line, the right gauge must be selected. Among the many instruments available, two commonly used ones are the compound gauge and the pressure gauge.
Both tools may look similar at a glance. They often share the same dial face, pointer, and casing. However, their functions and measurement ranges are quite different. Choosing the wrong gauge can lead to incorrect readings. This can cause safety problems, damage equipment, or reduce system efficiency.
Understanding the difference between a compound gauge and a pressure gauge helps engineers and technicians make informed choices. This article will explore both types in detail. It will also explain where each is used, how they are built, and why one might be chosen over the other.
What Is a Pressure Gauge?
A pressure gauge measures the force exerted by a fluid or gas within a system. This force is shown on the gauge dial in units such as psi, bar, or kPa. A standard pressure gauge only measures positive pressure. That means it reads pressure that is greater than atmospheric pressure. When the system is at rest or has no pressure, the pointer returns to zero.
Pressure gauges come in different types. The most common is the Bourdon tube gauge. In this design, the pressure moves a curved tube. As the tube straightens, the motion moves a needle to show the pressure reading. There are also other types such as the diaphragm pressure gauge. In that type, a thin membrane flexes to measure pressure.
Pressure gauges are widely used in systems that operate above atmospheric pressure. Examples include air compressors, water pumps, hydraulic lines, and steam systems. They help ensure that equipment is working within safe and efficient pressure limits.
What Is a Compound Gauge?
A compound gauge is designed to measure both pressure and vacuum. This means it reads pressure above and below atmospheric pressure. The scale on a compound gauge includes both positive and negative values. Usually, the negative side is marked in inches of mercury (inHg), and the positive side is marked in psi.
The compound gauge is useful in systems that shift between vacuum and pressure. It is commonly found in refrigeration systems, vacuum pumps, and other applications where pressure drops below atmospheric and then rises above it.
Like standard pressure gauges, compound gauges also use a mechanical sensing element. The most common is again the Bourdon tube. But the design allows it to measure vacuum as well as pressure. Some compound gauges also use diaphragm technology when more sensitivity is needed for low-pressure readings.
Key Differences Between Compound and Pressure Gauges
The first major difference is the range of measurement. A pressure gauge only reads values above zero. A compound gauge reads from negative to positive. This means a compound gauge is more versatile in certain systems.
The second difference is the scale. A pressure gauge shows one continuous range starting at zero and increasing. A compound gauge has two ranges. One moves from zero downward to show vacuum. The other moves from zero upward to show pressure.
A third difference is in application. Pressure gauges are used when only positive pressure needs monitoring. Compound gauges are used when both vacuum and pressure are present in the same system.
The choice depends on the system requirements. Using a pressure-only gauge in a vacuum system will result in incorrect or no readings. On the other hand, using a compound gauge in a high-pressure-only system may cause confusion or offer unnecessary range.
Construction and Mechanism
Most pressure and compound gauges are built with similar materials and components. These include a dial face, pointer, sensing element, and protective case. The difference lies in the internal design of the sensing mechanism.
In pressure gauges, the Bourdon tube is shaped and tensioned to react to positive pressure only. In compound gauges, the Bourdon tube or diaphragm is calibrated to respond to both vacuum and pressure. The linkage system must be precise to show accurate readings on both sides of the zero mark.
In sensitive applications, especially when measuring low-pressure ranges or in systems with corrosive media, a diaphragm pressure gauge may be preferred. This type of gauge uses a thin metal diaphragm that deflects under pressure. Diaphragm pressure gauges are available in both pressure-only and compound designs. They provide more stability and better resistance to vibration and clogging.
Common Applications for Pressure Gauges
Pressure gauges are used in a wide range of settings. These include manufacturing, power plants, HVAC systems, and fluid power systems. For example, a water pump system may use a pressure gauge to ensure flow remains within operating limits. If pressure drops or spikes, the operator can take action.
In industrial boilers, pressure gauges monitor steam pressure. In hydraulic systems, they help detect overloads or leaks. Because they measure only positive pressure, they are best suited for systems that do not fall below atmospheric conditions.
Common Applications for Compound Gauges
Compound gauges are often found in systems where vacuum and pressure both play a role. One major example is in refrigeration. When a cooling system starts, the pressure inside the lines may be below atmospheric. As the system warms or compresses the refrigerant, the pressure rises.
A compound gauge allows technicians to see the full cycle. It helps with charging refrigerants, testing for leaks, and ensuring that components are operating correctly.
Vacuum packaging systems and vacuum furnaces also use compound gauges. These devices must start in vacuum and then sometimes return to atmospheric or even positive pressure.
Calibration and Maintenance
Both compound gauges and pressure gauges need periodic calibration. Over time, mechanical wear, dirt, or fluid corrosion may affect the gauge accuracy. Calibrating ensures that readings remain reliable.
During calibration, a known pressure is applied. The gauge reading is then compared to the known standard. If needed, adjustments are made. In low-pressure applications or where high accuracy is needed, a diaphragm pressure gauge may be used as a reference. This is because it offers better sensitivity and stability in low pressure ranges.
Maintenance also includes cleaning, inspecting seals, and checking for damage. If a gauge is exposed to pressure spikes, it may lose calibration faster. Compound gauges must be especially checked for accuracy on both vacuum and pressure ranges.
Choosing the Right Gauge for the Job
Selecting between a compound gauge and a pressure gauge depends on your system’s needs. If the system operates only under positive pressure, a pressure gauge is the simple and cost-effective choice. If your system experiences vacuum conditions or fluctuates around atmospheric pressure, a compound gauge is necessary.
Consider the fluid being measured. If the medium is dirty, corrosive, or viscous, a diaphragm pressure gauge might be required. It provides isolation from the process fluid and maintains better performance under tough conditions.
Think about the scale needed. Too narrow a range may cause overpressure damage. Too wide a range may reduce accuracy. The goal is to match the gauge to the operating range of the system.
Conclusion: Function Defines the Instrument
While compound gauges and pressure gauges may look alike, their roles are different. A pressure gauge measures only above-atmosphere pressures. A compound gauge measures both vacuum and pressure. The difference lies in the range, the scale, and the application.
Each has its place in industrial systems. Engineers must evaluate system behavior and select accordingly. In sensitive or specialized systems, a diaphragm pressure gauge may also be preferred for its precision and durability.
Proper selection, use, and maintenance ensure that these instruments continue to serve reliably. Accurate pressure monitoring is not just a technical detail—it is a key to safety and performance.